Health, Safety and Environment

Health, safety and environmental philosophy Radio Network Solutions (RNS) is committed to providing employees, sub-contractors and visitors with a healthy and safe work environment. The primary objective of our policy is to develop an effective culture of prevention involving active participation by both the employer and the employees.
Health, safety and environmental policy The provisions of our policy apply to all RNS employees, and where applicable, external parties and/or sub-contractors performing work on behalf of and on RNS premises/sites.
RNS is committed to providing employees, sub-contractors and visitors with a healthy and safe work environment.
The primary objective of this policy is to develop an effective culture of prevention involving active participation by both the employer and the employees.
The right to a healthy and safe working environment is not expressly referred to in the Constitution, however, the right emerges from both the right to fair labour practices and, perhaps most significantly, the right of individuals to an environment that is healthy and not harmful to their health.
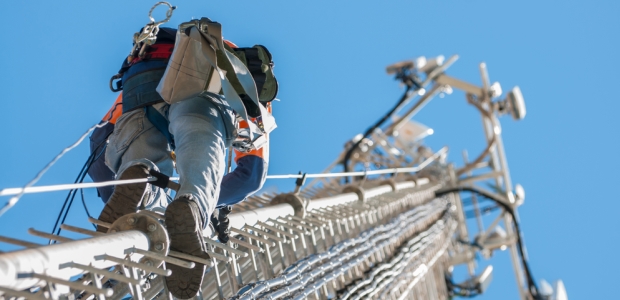
The ultimate responsibility for providing a safe working environment lies with RNS as an employer.
- Ensuring compliance to all relevant legislation pertaining to health, safety and the environment
- Regularly updating the identification of all new requirements pertaining to our activities
- Actively engaging all employees and contractors in health and safety matters
- Providing effective health and safety training
- Continuous assessment and responding to workplace hazards and risks
- Developing and implementing appropriate standards and procedures to mitigate risks identified
- Providing employees with safety equipment to carry out their duties in a healthy and safe manner
- Conducting intensified health and safety inspections and audit systems and providing environmental awareness training to all employees
- Set up a framework for identifying, implementing and monitoring objectives and targets with the focus on efficient health, safety and environmental systems
- By accepting that health and safety is as important as any other business activity
- Ensuring that every employee, sub-contractor and visitor understands that he/she is responsible for his/her own safety and those of others.
Health, safety, environmental vision and mission
In accordance with our Health, Safety and Environmental Policy statement and in line with legislation, to create, review and continuously update conceivable in-house Health, Safety and Environmental Policies and Procedures to support the RNS strategic plan in achieving an ISO accreditation. The primary objective is to ensure continuous quality, health, safety and environmental improvement in terms of the services we render to our customers and constantly re-aligning our strategies with our business partners to confirm that we are ideally positioned to offer a vast range of quality products and services varying from small private networks to some of the biggest telecommunications network companies including the African communications market to realise our overall vision to provide comprehensive turnkey services. To furthermore maximise opportunities in collaborating a partnership with our business partners, major clients and other support groups, we continuously monitor trends, realign our strategies and apply the necessary remedial action to ensure we mitigate all risks relating to health, safety and environmental deficiencies identified.
Internal accident/Incident reporting flowchart
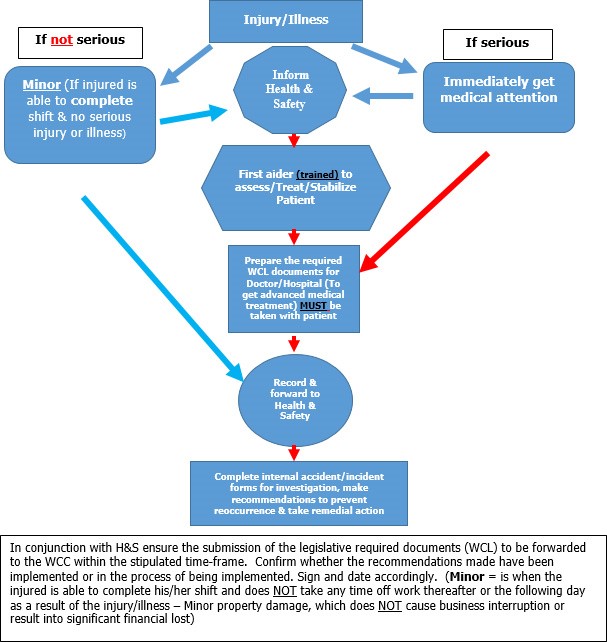
Internal emergency plan/Evacuation procedure
Our procedure is not a complete, step-by-step, how-to-do-it manual since each crisis is unique, with varying levels of threat and impact. However, our procedure applies to all RNS staff, visitors and contractors performing work on any site. It is important that the RNS appointed contractors use our procedure as a guide in order to incorporate and/or align the client’s (site where work is to be performed or conducted) or resident procedure, bearing in mind that each facility/site may pose its own and unique hazards and therefore presents different circumstances/potential hazards/dangers. In the unlikely event of an emergency or on the sound of an alarm, do NOT panic or attempt to take along anything, vacate the building by taking along any visitors/contractor (if any) exit via the SAFEST and shortest route. Assemble at the assembly point situated outside the entrance/exit gate and only return to your usual or normal place of work when instructed to do so by either your manager or the person in control of the emergency situation.
Smoking policy
The purpose of our policy is to create awareness of the risk associated with active and passive smoking in the workplace – thus, promoting a healthier, cleaner, safer, and more pleasant working environment. To improve the working relationships in the workplace – as tension between tobacco smokers and non-smokers would be reduced or removed. To create an enabling and supportive environment that provides an opportunity for smokers to cut down or quit smoking. To highlight the focus on general benefits of a smoke-free environment in the organisation, rather than highlighting the restrictions. The issue is smoking, not smokers and non-smokers. Whether people smoke or not is a personal matter, it is where they smoke that is an issue. RNS has a duty, in terms of the provisions of the Occupational Health and Safety Act (Act No. 85 of 1993) to provide a safe working environment and protect the health of all employees from illnesses and injuries arising from the workplace. Consequently, in the interest of the health and safety of all our employees, RNS moved towards a smoke-free work environment except in areas designated for smoking.
Health and safety committee
A Health and Safety Committee has been established in accordance with legislation. Given the nature of our business at RNS, all members of staff serve as a committee member and as a method for obtaining the required cooperation and understanding and to further assist us by serving as an effective culture of prevention involving active participation by both the employer and the employees at RNS. The Committee is chaired by our Managing Director (16.2 appointee) and facilitated by the Health and Safety manager. Meetings are held at intervals prescribed by the Act and attended by most staff as, many members of staff work and operate in remote areas, working on-site with sub-contractors to further ensure effective safety measures and efficient production methods are being adhered to at all times.
Material Safety Data Sheets (MSDS)
In accordance with the Occupational Health and Safety Act all chemicals, substances, lubricants or cleaning agents/products to be used in order to carry out any task shall be accompanied with the legislated required documents (MSDS). These documents contained important information entailing information such as the following:
- Storage, handling and usage requirements
- Steps to be taken in the unlikely event of a fire, first aid requirements etc.
- Personal Protective Equipment (PPE) requirements
- Environmental emergencies such as a chemical spill, chemical release etc.
- Performing due diligence.
Contractor selection and appointment
In accordance with the Occupational Health and Safety Act and in line with our Health and Safety policy, RNS takes extreme care in the selection and appointment of contractors, contracted to perform work. Contractors project the image, reputation, work, safety standard, as well as the professionalism of RNS therefore, it is our responsibility and in our interest to ensure that the most suitable contractor is appointed. To ensure the latter is achieved, the following non-negotiable selection criteria aspects are carefully taken into consideration, prior to being formally appointed:
- Company registration
- Letter of Good Standing (Registered with the Department of Labour)
- The legislative health and safety appointments (i.e. 16.1; 16.2; Health and Safety Reps) etc.
- Documented health and safety plan
- Up-to-date health and safety training records
- Written policies and procedures
- Documented risk assessment for every task to be performed
- Insurance registration and history
- History of health and safety related incidents and/or accidents
- Safe work procedures
- Waste management systems
- Pollution management or prevention systems
- Vehicle maintenance and training records of drivers
- Security checks on all employees
- Medical surveillance on management and staff
- Consequence management
- Provision of site safety files completed and submitted for scrutiny.
Working at heights
To ensure the safety of all persons required for any kind of work to be carried out on non-fixed and/or non-protected surfaces, platforms and/or structures at heights of two (2) metres or higher strict requirement must be met. RNS conforms to the requirement of each client as requirements for each site are unique provided that the basic regulations are adhered to.
The following represent some of the minimum requirements applicable to all persons required to work at heights:
- A detailed description of the work to be done
- The date, time and duration of the permit (proportional to the nature and potential risk of each activity - maximum three (3) months for routine and low risk activities in connection with one project or maximum one (1) year for special qualified employees (list to be available))
- The one (1) year permit shall only be applied in agreement with the Health and Safety Manager
- Appropriate sign-offs
- Inspection of the equipment to be used (e.g. ladder, scaffolding, trestles, etc.)
- Required Personal Protective Equipment (PPE) (e.g. body harness, deceleration devices, etc.)
- Isolation of the area below
- Required risk control measures and emergency response procedures
- A list of people authorised to approve the permits (“Authorised Persons”)
- Workers assigned to work at heights shall undergo initial and periodical medical assessments
- Workers assigned to work at heights shall be provided with initial and regular refresher training on the specific risks and required control measures
- Appropriate fall protection devices (e.g. body harness with lifelines to be fixed at each anchorage, etc.) shall be used for employees assigned to work at heights
- Fixed walking and working surfaces, platforms and/or structures at heights of two (2) metres or higher shall be protected with guardrails (including top-rail, mid-rail and toe-boards)
- Accesses to roof areas, non-fixed and/or non-protected surfaces, platforms and/or structures at heights of two (2) metres or higher shall be restricted to authorised personnel only
- Documentation and records regarding all requirements included in this procedure (permit system, medical assessments, training, etc.) shall be kept for at least one (1) year or based on legal requirements
- Where the work to be performed at height includes other specific hazards (such as hazardous materials handling, hot work, confined space, electrical hazards, etc.), the correspondent applicable health and safety procedures shall be followed in addition to the specific control measures related to working at heights.
Training and awareness
We have developed, implemented, and administer an on-going Occupational Health and Safety education and awareness programme for all our employees. RNS Management is responsible for ensuring that all our employees and appointed contractors fully participate in our programme as we believe that training for all our employees enable them to perform their tasks safely in and in accordance with the legislated standard and includes:
- The relevant provisions of OHSA and the concurrent regulations
- The implementation of risk control measures and/or procedures
- Industry specific standards.
Contact us
The above serves as a summary and contains some of the important Health, Safety and Environmental related Policies, Procedures and Requirements relating or applicable to all employees or contractors performing work for/at RNS. For further information regarding any Health, Safety or any Environmental related matters, contact the RNS Health and Safety division at Kurt@radionetwoksolutions.com
Download PDF (229 KB)